1. INTRODUCTION
Washington State University’s (WSU) Laser Safety Program is a tool designed to provide assistance for WSU laboratories using laser devices in order to protect Faculty, Staff, employees and students from the hazards associated with their presence and use.
The laser safety policy SPPM 4.50 is based on standards promulgated by Washington Administrative Code (WAC) 296-62-09005, ANSI Z136.1, and applies to all lasers and laser systems, whether purchased, borrowed, fabricated, or brought in for use by others. Refer to SPPM 4.50 for formal guidelines. This section of the Laboratory Safety Manual is meant to provide basic information on laser operation and safety practices only.
Many lasers are capable of causing eye injury to anyone who looks directly into the beam. Reflections alone from high-power laser beams can produce permanent eye damage. High-power laser beams can also burn exposed skin. Laser operators must be aware of other potential dangers such as fire, electrical, biological and chemical hazards.
The Laser Safety Program Template, Appendix Q, was created to assist with the development of an individualized Laser Safety Program specific to an area using lasers. It is not an instruction manual for the use of lasers. The PI / supervisor (Laser Safety Officer) responsible for the laser must provide laboratory specific details in order to complete the Program/Template. While it is obvious that the safe use of all classes of lasers is encouraged, Class 3 and 4 lasers must have a Laser Safety Program in place. The Laser Safety Program Template is available to assist the PI/Supervisor with the development of their individual Laser Safety Program for Class 3 and 4 lasers. If further assistance or information is needed, contact Environmental Health and Safety at 509-335-3041.
Responsible Parties
- Principal InvestigatorThe Principal Investigator or Laboratory Supervisor is responsible for:
- Providing laser specific training for all operators.
- Ensuring each assigned laser is operated safely and in accordance with applicable requirements.
- Ensuring that each laser is stored securely and safely when not in use so that it is not usable by unauthorized personnel or under unauthorized conditions.
- Maintaining written SOPs for Class 3B (if required) and all Class 4 lasers and ensuring laser use is commensurate with the requirements of the SOP.
- Reporting any known or suspected accidents.
- Ensuring that a hazard assessment for personal protective equipment (PPE) use and specific PPE training is provided for all laser users for whom PPE will be required.
- Laser Safety OfficerThe Laser Safety Officer will be responsible for:
- Maintaining inventory of all Class 3B and Class 4 lasers and verifying classification if necessary.
- Reviewing standard operating procedures, alignment procedures and other control measures, before initial use.
- Periodically inspect Class 3B and Class 4 lasers to assess compliance with safety requirements.
- Providing assistance in evaluating and controlling hazards.
- Maintaining records of Class 3B and Class 4 laser inspections.
- Participating in accident investigations involving lasers. Suspending, restricting or terminating the operation of a laser or laser system without adequate hazard controls.
- Maintaining a safe environment/area during the operation of a laser.
- Ensuring training requirements are completed and documentation is maintained as required.
- The Laser Safety Officer and Laser Operator are often the same person and may be the Laboratory PI or Manager.
- Laser OperatorThe laser operator is responsible for:
- Completing all applicable requirements before operating a laser.
- Operating lasers safely and in a manner consistent with safe laser practices, requirements and standard operating procedures.
- Environmental Health and Safety (EH&S)Environmental Health and Safety is responsible for:
- Updating information regarding the use of lasers as it becomes available
- Assisting laser containing laboratories with determining the maximum permissible exposure limit (MPE), nominal hazard zone (NHZ), personal protective equipment (i.e., eye protection – optical density, skin protection, etc.); and non-beam hazards as requested;
- Assisting laser containing laboratories with the implementation of the Laser Safety Program in any given area as requested (i.e. assisting with: the creation of the laser safety plan, determining correct signage, reviewing safety measures, reviewing labeling and reviewing engineering controls in place).
2. LASER CHARACTERISTICS
The term LASER is an acronym for Light Amplification by the Stimulated Emission of Radiation.
Lasers operate by the excitation of a medium through the introduction of energy. As electrons in this medium return to their ground state, they stimulate the release of light of a certain wavelength. This chain reaction continues until a certain number of photons reach the totally reflective mirror. This reverses the direction of the beam and the beam continues to intensify until it passes through the partially transmissive mirror, constituting the laser beam.
Laser radiation will continue to be produced as long as energy is applied to the lasing medium. Laser radiation differs from normal light in that it is coherent, electromagnetic radiation characterized by one or more specific wavelength(s). The wavelengths are determined primarily by the composition of the lasing medium, which can be a solid, liquid, or gas. Laser radiation may be emitted in the visible portion of the electromagnetic spectrum (wavelengths of 400 – 700 nm) or in the invisible infrared (700-3×106 nm) and ultraviolet (180-400 nm) regions. Laser radiation transmits energy which, when a laser beam strikes matter, can be transmitted, absorbed, or reflected. If a material transmits a laser beam it is said to be transparent. If the beam is not transmitted, the material is said to be opaque and the incident radiation is absorbed or reflected.
A. Absorption
Absorbed laser energy appears in the target material as heat. Absorption and transmission are functions of the chemical and physical characteristics of the target material and the wavelength of the incident radiation. At visible wavelengths, laser radiation impinging on the eye is focused on the retina and, if sufficient energy is absorbed, can cause cell destruction. At longer and shorter wavelengths, such as the far infrared and the ultraviolet, radiation striking the eye is absorbed in the cornea and the lens rather than being focused on the retina. Although these structures are less easily damaged than the retina, excessive energy absorption can cause cell damage and impairment of vision.
B. Reflection
Reflection is a function of the physical character of the surface of the target material. A smooth polished surface is generally a good, or specular, reflector; a rough uneven surface usually is a poor reflector producing a diffuse reflection. A reflector such as a flat mirror changes the direction of an incident beam with little or no absorption. A curved mirror or surface will change the divergence angle of the impinging laser beam as well as its direction.
For a diffuse reflection, the reflected energy is scattered in all directions thereby reducing the energy or power density. Generally, diffusely reflecting surfaces are favored when designing a laser experiment since their use reduces the likelihood of a specular reflection and hence enhances the safety of the experiment. Simple examples of forms of protection include, painting surfaces Matte black to decrease reflection, covering metal beams with non reflective materials or welding blankets, removing rings and other jewelry prior to working with lasers.
C. Transmission
Most visible light laser beams, such as those generated by HeNe, Nd:Yag, and Krypton lasers are transmitted through clear objects, such as a room window or water. Use of these types of lasers often requires the use of window coverings that absorbs the beam and prevents the laser hazard from existing outside of the immediate work area. It is important to note that these coverings will need to be fire resistant for use with higher- powered lasers. Some lasers, such as CO2, are not transmitted through glass, and therefore do not require the use of window coverings.
3. LASER CLASSIFICATION
To provide a basis for laser safety requirements, all lasers and laser systems in the United States are classified according to the ANSI Z136.1 standard and the Federal Laser Products Performance Standard (FLPPS). The manufacturer is responsible for determining the laser classification. The builder must classify custom-built and modified lasers. The ANSI Z136.1 standard is enforced by the Occupational Safety and Health Administration (OSHA). The Laser Products Performance Standard is enforced by the Centers for Devices and Radiological Health (CDRH), a part of the Food and Drug Administration (FDA). The following section describes the classification for continuous-wave lasers. The same hazard levels also apply to pulsed lasers with pulse duration of less than 0.25 seconds but classification is more complex.
A. Class 1, 1M Lasers
Class 1 lasers are low-powered (less than 1mW) and do not emit hazardous radiation under normal operating conditions because they are completely enclosed. Class 1 lasers are exempt from any control measures. Equipment, such as laser printers and laser disc players, are examples of this class. These lasers may present hazards if the housing is breached for maintenance (See Embedded Lasers).
D. Class 3B Lasers
Class 3B lasers are systems with power levels of 5 mW to 500 mW for continuous wave lasers or less than 10 J/cm2 for a 0.25 s pulsed laser. These lasers produce an eye hazard if viewed directly. This includes intrabeam viewing or specular reflections. Higher power lasers in this class will also produce hazardous diffuse reflections. See the specific usage requirements for Class 3B lasers.
B. Class 2, 2M Lasers
Class 2 lasers are visible continuous wave (CW) and repetitive-pulse lasers or laser systems which can emit accessible radiant energy exceeding the appropriate Class 1 AEL but less than 1 mW. The human aversion response or blink reflex, which occurs within 0.25 seconds, provides adequate protection for Class 2 lasers. However, it is possible to overcome the aversion response and stare into the Class 2 laser long enough to damage the eye. Class 2 lasers are typically exempt from control measures other than having a protective housing and label. Equipment such as some visible continuous wave Helium-Neon lasers and some laser pointers are examples of Class 2 lasers.
E. Class 4 Lasers
Class 4 lasers are systems with power levels greater than 500 mW for continuous wave lasers or greater than 10 J/cm2 for a 0.25 s pulsed laser. These lasers may produce eye, skin and fire hazards through intrabeam viewing, specular or diffuse reflections and the direct beam itself. See the specific usage requirements for Class 4 lasers for further information.
C. Class 3R Lasers
Class 3R lasers are systems with power levels of 1 to 5 mW that normally would not produce a hazard if viewed for only momentary periods with the unaided eye. They can pose severe eye hazards when viewed through optical instruments (e.g., microscopes, binoculars, or other collecting optics). Class 3R lasers must be labeled. Equipment, such as some visible continuous wave Helium-Neon lasers and some solid state laser pointers, are examples of Class 3R lasers. It is recommended that no pointers over Class 3R be used.
F. Embedded Laser
Embedded lasers are found in laser products with lower class ratings. Laser printers, CD players, and laser welders may have Class 3B or Class 4 lasers in their protective and interlocked housings. When such a laser system is used as intended, the lower laser class applies. When such a system is opened (e.g., for service or alignment) and the embedded laser beam is accessible, the requirements for the higher class of the embedded laser must be implemented.
Type |
Description |
Examples |
Beam Hazard |
Class 1 | Completely enclosed or very low power (0.4 W for visible lasers) | CD player, laser printer | Incapable of causing injury during normal operation. |
Class 1M | Completely enclosed or very low power (0.4 W for visible lasers) | Laser scanners, etchers | Incapable of causing injury unless collecting optics are used |
Class 2 | Visible lasers emitting less than 1mW radiant power | Some laser pointers | Visible lasers incapable of causing injury in .25 seconds. |
Class 2M | Visible lasers emitting less than 1mW radiant power | Laser levels, survey equipment | Visible lasers incapable of causing injury in .25 seconds unless collecting optics are used. |
Class 3R | 1 to 5 mW | Most alignment lasers and laser pointers | Marginally unsafe for intrabeam viewing; up to 5 times the class 2 limit for visible lasers or 5 times the class 1 limit for invisible lasers. |
Class 3B | Output power between 5 and 500 mW. | Analytical and research applications, embedded lasers | Eye hazard for intra beam viewing |
Class 4 | Above 500 mW | Surgical lasers, cutting, welding, research lasers | Eye and skin hazard for both direct and scattered exposure. |
4. LASER SAFETY HAZARDS
A. Beam Hazards
The nature of laser beam damage and the threshold levels at which each type of injury may occur depends on several parameters. These include wavelength of light, energy of the beam, divergence and exposure duration. For pulsed lasers, parameters also include the pulse length, pulse repetition frequency and pulse train characteristics. ANSI Z136.1 standard establishes Maximum Permissible Exposure (MPE) limits for laser radiation. MPE’s need to be determined for each specific laser so that a Nominal Hazard Zone (NHZ) can be established. The Nominal Hazard Zone is the area around a laser in which the applicable MPE is exceeded. EH&S is available to assist with determining MPEs and NHZs. When an MPE is exceeded, damage can occur to the skin, retina, lens, cornea, and conjunctival tissue surrounding the eye (See Fig. 1). For lasers over 500 mW, the beam has the potential to ignite flammable materials and start a fire.
Thermal burns, acoustic damage, and photochemical damage to the retina may occur from laser light in the near ultraviolet (UV), visible and near infrared (IR) regions (below 400 nm – 1400 nm). Damage occurs as the laser light enters the eye and is focused on the retina. Normal focusing of the eye amplifies the irradiance by approximately 100,000; thus, a beam of 1 mW/cm2 results in an exposure of 100 W/cm2 to the retina. Energy from the laser beam is absorbed by tissue in the form of heat, which can cause localized intense heating of sensitive tissues. The most likely effect of excess exposure to the retina is thermal burn that destroys retinal tissue. Since retinal tissue does not regenerate, the damage is permanent, which may result in the loss of sight in the damaged area.
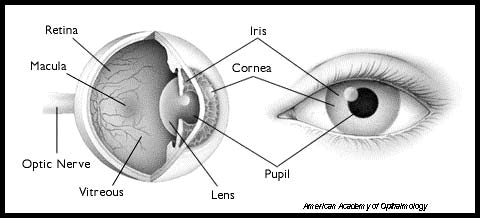
Fig. 1 Anatomy of the Human Eye
Intrabeam viewing of the direct beam and the specularly reflected beam are most hazardous when the secondary reflector is a flat and polished surface (mirror-like). Secondary reflections from rough uneven surfaces produce more diffuse or scattered reflections and are usually less hazardous. Extended source viewing of normally diffuse reflections are not normally hazardous except for very high power lasers (Class 4 lasers). Extra care should be taken with IR lasers since diffuse reflectors in the visible spectrum may reflect IR radiation differently and produce greater exposures than anticipated.
The figures below represent the ways in which laser light can be viewed
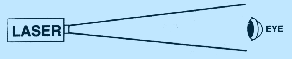
Fig.1. Intrabeam viewing of direct (primary) beam. This type of viewing is most hazardous
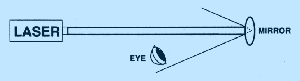
Fig.3. Intrabeam viewing of a specularly reflected (secondary) beam from a curved surface reflector, less hazardous than that of a flat source reflection.
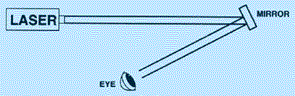
Fig. 2. Intrabeam viewing of a specularly reflected (secondary) beam from a flat surface reflector. Specular reflections are most hazardous when the reflecting surface is flat.
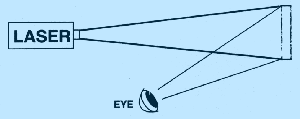
Fig.4. Extended source viewing of a normally diffuse reflection. Diffuse reflections are not normally hazardous, except with very high power Class 4 lasers.
B. Work Area Safety Practices
- A laser should be isolated from public areas. Doors should be closed or locked to keep out unauthorized personnel. The proper warning signs should be posted.
- The illumination in the area should be as bright as practicable in order to constrict the eye pupils of users.
- The laser should be set up so that the beam path is above or below normal eye level (below 4.5 ft. or above 6.5 ft.).
- Where practical, the laser system or beam should be enclosed to prevent accidental exposure to the beam.
- The potential for specular reflections should be minimized by shields and by removal of all unnecessary shiny surfaces.
- Windows to hallways or other outside areas must be provided with adequate shades or covers when necessary to keep the Nominal Hazard Zone (NHZ) within the room.
- The main beams and reflected beams should be terminated or dumped. This is required for any accessible laser for which the MPE limit could be exceeded.
- Electrical installation must meet electrical safety standards. The active laser never should be left unattended unless it is a part of the controlled environment.
- Warning devices must be installed for lasers with invisible beams to warn of operation.
- The laser work area should be maintained as free of clutter as possible, to minimize the chance of accidentally igniting something.
- Ensuring that lasers are well secured to the work surface helps prevent a stray beam.
C. Safe Laser Use Practices
- Avoid looking directly at the beam at all times.
- Do not aim the laser with the eye; direct reflections could cause retinal damage.
- Avoid looking at the pump source.
- Clear all personnel from the anticipated path of the beam.
- Before operating the laser, warn all personnel and visitors of the potential hazard, and ensure all safety measures are satisfied.
- Be very cautious around lasers that operate at frequencies not visible to the human eye.
- Do not wear bright, reflective jewelry or other objects, they may become a reflective source.
- Use appropriately rated optical density eye protection when working with a Class 3B or Class 4 laser. Eye protection is specific for the type of laser and may not protect at different frequencies or powers. Frequent inspection of protective eyewear to ensure that glasses are not pitted or scratched is needed to ensure they will provide adequate protection. Remember that eye protection does not shield from the beam unless they are worn.
5. LASER USAGE REQUIREMENTS
A. General Requirements
Class 1 and 2 lasers may be used for the intended purposes of their manufacturer without restrictions. Any direct eye exposure to these types of lasers should be avoided.
Class 3R, Class 3B, and Class 4 shall carry a warning label containing the laser classification, type, and other warnings required by ANSI Z136.1 or assign an equivalent level by the builder. These requirements also apply to non-commercially built lasers that are used at Washington State University campuses.
All laser operators must complete training specific to the type of laser they operate.
All lasers must be operated according to the applicable ANSI Z136.1 safety standards and in a manner consistent with safe laser practices. Laser Safety Standard Operating Procedures (SOPs) are required for Class 3B lasers and for all Class 4 lasers.
Each Class 3B and Class 4 laser shall be used in a controlled area that restricts access to unauthorized personnel. The controlled laser areas must be posted with appropriate warning signs.
Each operator of a Class 3B or Class 4 laser must wear protective equipment (e.g., eye wear and clothing) as appropriate.
B. Engineering Controls
All lasers require a protective housing.
All Class 3B and Class 4 lasers must be equipped with engineered safety features such as:
- Protective housing interlock system that prevent emission of laser radiation when the housing is open.
- Viewing portals in the protective housing must be equipped with filters and attenuators that keep escaping light below the Maximum Permissible Exposure (MPE) limit.
- Optical instruments for viewing the laser system must be equipped with filters and attenuators and interlocks to keep exposures below the MPE limit for all conditions of operation and maintenance.
- Class 4 lasers shall also be equipped with a removable master key switch if provided by the manufacturer. The laser shall not be operable when the key is removed.
- The lasers should be equipped with electrical connections that allow for an access control system and remote shut-off devices. When the terminals are open-circuited, the laser must not emit any radiation in excess of the MPE. Class 4 laser systems must be equipped with an integral and permanently attached beam stop or attenuator capable of preventing the emission of laser light in excess of the MPE limit when the beam is not required.
C. Class 3B and 4 Laser Controlled Area
The following items are required for Class 3B laser controlled areas:
- Posted with the appropriate warning sign(s).
- Operated by qualified and authorized personnel.
- Under the direct supervision of an individual knowledgeable in laser safety.
- Have any potentially hazardous beam terminated in a beam stop of an appropriate material.
- Have only diffuse reflective materials in or near the beam path, where feasible.
- Have personnel within the controlled area provided with the appropriate eye protection if there is any possibility of viewing the direct or reflected beams.
- Have the laser secured such that the beam path is above or below eye level of a person in any standing or seated position, except as required for medical use.
- Have all windows, doorways, open portals, etc. from an indoor facility be either covered or restricted in such a manner as to reduce the transmitted laser radiation to levels at or below the appropriate ocular MPE.
- Require storage or disabling (for example, removal of the key) of the laser or laser system when not in use to prevent unauthorized use.
In addition to the items listed for Class 3B areas, the following are required for Class 4 lasers:
- Personnel who enter a Class 4 controlled area during laser operation shall be adequately trained, provided with appropriate protective equipment, and follow all applicable administrative and procedural controls.
- Class 4 area/entryway safety controls shall be designed to allow both rapid egress by laser personnel at all times and admittance to the laser controlled area under emergency conditions.
- For emergency conditions there shall be a clearly marked “Panic Button” (remote controlled connector or equivalent device) available for deactivating the laser or reducing the output to the appropriate MPE levels.
- Area or entryway safety controls to deactivate the laser or reduce the output to the appropriate MPE levels in the event of unexpected entry into the laser controlled area.
- These controls may be non-defeatable, defeatable or procedural as determined by the LSO.
- Temporary Laser Controlled Area
Where removal of panels or protective housings, over-riding of protective housing interlocks, or entry into the NHZ becomes necessary (such as for maintenance and service) a temporary laser controlled area shall be set up. The temporary laser controlled area shall be posted on the outside with a Notice sign and with the appropriate warning sign (Class 3B or Class 4) inside the controlled area to warn of the potential hazard.
6. PERSONAL PROTECTIVE EQUIPMENT
In addition to engineering and administrative controls, personal protective equipment for skin and/or eyes is often necessary when working with Class 3B or Class 4 lasers.
A. Eye Protection
Eye protection suitable to the laser must be provided and worn within the laser control area if there is a potential for exceeding the MPE limit if the beam is viewed. Protective eyewear may include goggles, face shields, spectacles or prescription eyewear using special filter materials or reflective coatings.
No single type of eyewear will provide protection against all wavelengths of laser radiation; therefore, eye protection should:
- Provide enough visibility to move about safely.
- Be able to withstand the maximum power of laser radiation likely to be encountered.
- Be able to absorb the specific wavelength of radiation that is being used.
- Be clearly labeled with wavelength they are designed for, the optical density at that wavelength, together with the maximum power rating.
- Be inspected periodically by the laser operator to ensure that pitting, cracking and other damage will not endanger the wearer.
Lasers that can be tuned through a range of wavelengths present special problems. Broad band laser goggles may provide the level of protection required but they must be chosen with great care. Contact EH&S at 509-335-3041 for assistance with choosing the correct protective equipment.
B. Skin Protection
Skin injuries from lasers primarily fall into two categories: thermal injury (burns) from acute exposure to high power laser beams and photochemically induced injury from chronic exposure to scattered ultraviolet laser radiation.
Thermal injuries can result from direct contact with the beam or specular reflections. These injuries (although painful) are usually not serious and are normally easy to prevent through proper beam management and hazard awareness.
Photochemical injury may occur over time from ultraviolet exposure to the direct beam, specular reflections, or even diffuse reflections. The effect can be minor or severe sunburn, and prolonged exposure may promote the formation of skin cancer. Proper protective eyewear and clothing may be necessary to control UV skin and eye exposure.
Clothing such as gloves and covers for the forearms may be required to protect the skin if laser intensity and wavelength warrant such protection. This is most important if the laser is running in the ultra-violet. Very large peak powers with pulsed ultra-violet laser can be particularly dangerous.
Other protective equipment includes window drapes designed to prevent the escape of the laser beam outside of the room that it is in. The type of drape used must be appropriate to the laser. Some laser beams such as that from a CO2 laser do not penetrate glass and therefore do not require the use of window drapes.
Contact EH&S at 509-335-3041 for further information on protective equipment.
NOTE: All employees required to wear personal protective equipment must undergo a certified hazard assessment for PPE use and receive specific PPE training per Washington State Department of Labor and Industries regulations. This assessment and training is the responsibility of the individual PI/lab supervisor. Please contact EH&S at 509-335-3041 for further information.
7. WARNING LABELS AND SIGNS
ANSI Z136.1 requires that lasers and laser systems have appropriate warning labels and that the areas in which they operate be posted with appropriate warning signs. For further information contact EH&S at 509-335-3041. The figures below are examples of laser warning signs:
8. LASER SAFETY STANDARD OPERATING PROCEDURES (SOP)
A written SOP is required for Class 3B and 4 lasers.
See
Appendix Q for a template and example of a completed Laser SOP.
9. LASER SAFETY TRAINING
All Class 3B or Class 4 laser users are required to complete laser safety training. EH&S is available to assist with development of your laboratory specific training programs and offers templates, guides and canned presentations for adaption to your needs. See the Laboratory Safety web page or call 509-335-3041 for further information.
In addition, all laser operators must be trained on the usage of each specific laser to be used. The Principal Investigator, vendor, or other qualified individual may provide this training. Records of this training must be maintained.
Before operating a Class 3B, Class 4 laser, or an embedded Class 3B or Class 4 laser with the protective housing removed, a person must:
Review the Laser Safety Guide for that laboratory.
Receive from the Principal Investigator a thorough review of the laser equipment to be used and the administrative requirements, alignment procedures and applicable SOPs.
Review the operating and safety instructions furnished by the manufacturer.
Utilize appropriate personal protective equipment.
10. EXPOSURE INCIDENTS
If an exposure incident occurs, the affected individual(s) must inform their supervisor and an
Online Incident Report Form must be completed and submitted online within 24 hours. Failure to do so may result in a denial of the claim. If the incident occurs outside of regular clinic hours, individual(s) should be seen at the Emergency Room. A
Supervisor’s Accident Investigation Report may also be necessary.
11. ASSOCIATED HAZARDS
A. Electrical Hazards
The most lethal hazard associated with lasers is the high voltage electrical system required to power lasers. Several deaths have occurred when commonly accepted safety practices were not followed by persons working with high voltage sections of laser systems. Lockout Tagout (LOTO) training is required before performing any work on energized sources. For further information on LOTO training contact EH&S at 509-335-3041.
The following is a list of recommended electrical safety practices:
- Only authorized and trained individuals may perform electrical tasks, check with your supervisor prior to conducting any work on electrical systems.
- Do not wear rings, watches or other metallic apparel when working with electrical equipment.
- When working with high voltages, regard all floors as conductive and grounded.
- Do not handle electrical equipment when hands or feet are wet or when standing on a wet floor.
- Be familiar with electrocution rescue procedures and emergency first aid.
- Prior to working on electrical equipment, de-energize the power source. Only trained personnel are authorized to perform LOTO procedures. Lockout and tag-out the disconnect switch.
- Check that each capacitor is discharged and grounded prior to working in the area of the capacitors.
- Use shock preventing shields, power supply enclosures, and shielded leads in all experimental or temporary high-voltage circuits.
B. Laser Generated Airborne Contaminants (LGAC)
Laser Generated Airborne Contaminants (LGAC) are air contaminants associated with the use of Class 3B and Class 4 lasers. LGACs result from the interaction of the laser beam with target or other materials and can include metallic fumes and dust, chemical fumes and aerosols containing biological contaminants. Some examples of LGAC that may be generated include benzene, anthracene and biphenyl.
Many dyes used as lasing media are toxic, carcinogenic, corrosive or pose a fire hazard. A chemical inventory and safety data sheet (SDS) must be available in the laboratory’s Chemical Hygiene Plan. Further assistance in developing a specific Chemical Hygiene Plan is available from EH&S.
Various gases might be exhausted by lasers or produced by targets. Proper ventilation is required to reduce exposure levels of the gas products below acceptable limits.
Cryogenic fluids are used in the cooling systems of certain lasers. As these materials evaporate, they replace the oxygen in the air; thus, adequate ventilation must be ensured. Cryogenic fluids are potentially explosive when ice collects in valves or connectors that are not specifically designed for use with cryogenic fluids. Although the quantities of liquid nitrogen used are small, protective equipment may be required to prevent freeze burns.
In addition, compressed gases used in lasers may also present potential health and safety hazards. Problems may arise when working with unsecured cylinders, cylinders of hazardous materials not maintained in ventilated enclosures, and gases of different categories (toxins, corrosives, flammables and oxidizers) are stored together. Contact EH&S for further information at 509-335-3041.
C. Collateral Radiation
Radiation other than that associated with the primary laser beam is called collateral radiation. Examples are X-rays, LTV, plasma, radio frequency emissions, and ionizing radiation. X-rays could be produced from two main sources in the laser laboratories: Electric-discharge lasers and high-voltage vacuum tubes of laser power supplies, such as rectifiers, thyratrons and crowbars. Any power supplies that require more than 15 kilovolts (kV) may produce enough X-rays to cause a health hazard. Interaction between X-rays and human tissue may cause a serious disease such as leukemia or other cancers, or permanent genetic effects that may show up in future generations.
D. Fire Hazards
Class 4 lasers represent a fire hazard. Depending on the construction material, beam enclosures, barriers, stops and wiring are all potentially flammable if exposed to high beam irradiance for more than a few seconds.
E. Explosion Hazards
High-pressure arc lamps, filament lamps and capacitors may explode violently if they fail during operation. These components are to be enclosed in a housing that will withstand the maximum explosive force that may be produced. Laser targets and some optical components also may shatter if heat cannot be dissipated quickly enough. Consequently care must be used to provide adequate mechanical shielding when exposing brittle materials to high intensity lasers. Liquid nitrogen may explode under certain conditions.
12. GLOSSARY
Aversion Response (Blink Response) – The closure of the eyelid or movement of the head to avoid exposure to a noxious stimulant of bright light. It generally occurs within 0.25 seconds, which includes the blink reflex time.
Continuous Wave (CW) – The output of a laser, operated in a continuous rather than a pulsed mode. For purposes of safety evaluation, a laser that is operated with a continuous output for a period of 0.25 seconds or greater is regarded as a CW laser.
Controlled Area – An area where the occupancy and activity of those within is subject to control and supervision for the purpose of protection from laser radiation and related hazards.
Diffuse Reflection – Change of spatial distribution of a beam of radiation when it is reflected in many directions by a surface or by a medium.
Energy – The capacity for doing work. Energy content is commonly used to characterize the output from pulsed lasers and is generally expressed in Joules (J).
Fail-Safe Interlock – An interlock where the failure of a single mechanical or electrical component of the interlock will cause the system to go into, or remain in, a safe mode.
Infrared Radiation – Electromagnetic radiation with wavelengths that lie within a range of 700 nm to 1 mm.
Intrabeam Viewing – The viewing condition whereby the eye is exposed to all or part of a laser beam.
Irradiance (E) – Radiant power incident per unit area upon a surface, expressed in watts per square centimeter (W/cm2).
Laser – Light Amplification by Stimulated Emission of Radiation. A device that produces an intense, coherent, directional beam of light by stimulated emission of electronic or molecular transitions to lower energy levels.
Laser Operator – An individual who has met all applicable laser safety training and approval requirements for operating a laser or laser system.
Maximum Permissible Exposure (MPE) – The level of laser radiation to which a person may be exposed without hazardous effect or adverse biological changes to eye or skin. MPE is expressed in terms of either radiant exposure (Joules/cm2) or irradiance (Watts/cm2). The criteria for MPE are detailed in Section 8 of ANSI Z136.1.
Nominal Hazard Zone (NHZ) – The space within which the level of the direct, reflected, or scattered radiation during normal operation exceeds the applicable MPE. Exposure levels beyond the boundary of the NHZ are below the appropriate MPE level.
Optical Density (Di) – Logarithm to the base ten of the reciprocal of the transmittance: Di = log T, where T is the transmittance.
Power – The rate at which energy is emitted, transformed, or received in Watts/second or Joule/second. Also called the radiant power.
Principal Investigator – The individual who is responsible for the laboratory space.
Pulsed Laser – A laser that delivers its energy in the form of a single pulse or a train of pulses. The duration of a pulse is regarded to be less than 0.25 seconds.
Q-Switched Laser – A laser that emits short (~30 nanoseconds), high-power pulses by means of a Q-switch. A Q-switch produces very short, intense laser pulses by enhancing the storage and dumping of electronic energy in and out of the lasing medium, respectively.
Radiant Exposure (H) – Surface density of the radiant energy received (Joules/cm2).
Radiant Flux (F) – Power emitted, transferred, or received in the form of radiation, expressed in Watts (also called radiant power).
Repetitively Pulsed Laser – A laser with multiple pulses of radiant energy occurring in sequence with a frequency of 1 Hz.
Specular Reflection – A mirror-like reflection typically resulting from a shiny, flat surface.
Standard Operating Procedure (SOP) – A set of operating instructions. The procedure specifies measures which, if followed, will ensure safe and correct use or performance of a task or procedure (such as operating a laser or laser system, or use of a chemical).
Transmittance – The ratio of total transmitted radiant power to the total incident radiant power.
Ultraviolet Radiation (Light) – Electromagnetic radiation with wavelengths smaller than those of visible radiation; for the purpose of laser safety, 180 nm to 400 nm.
Visible Radiation (Light) – Electromagnetic radiation that can be detected by the human eye. This term is commonly used to describe wavelengths that lie in the range of 400 nm to 700 nm.
Watt – The unit of power or radiant flux. 1 watt = 1 Joule per second.
Wavelength – The distance between two successive points on a periodic wave that have the same phase.
13. REFERENCES